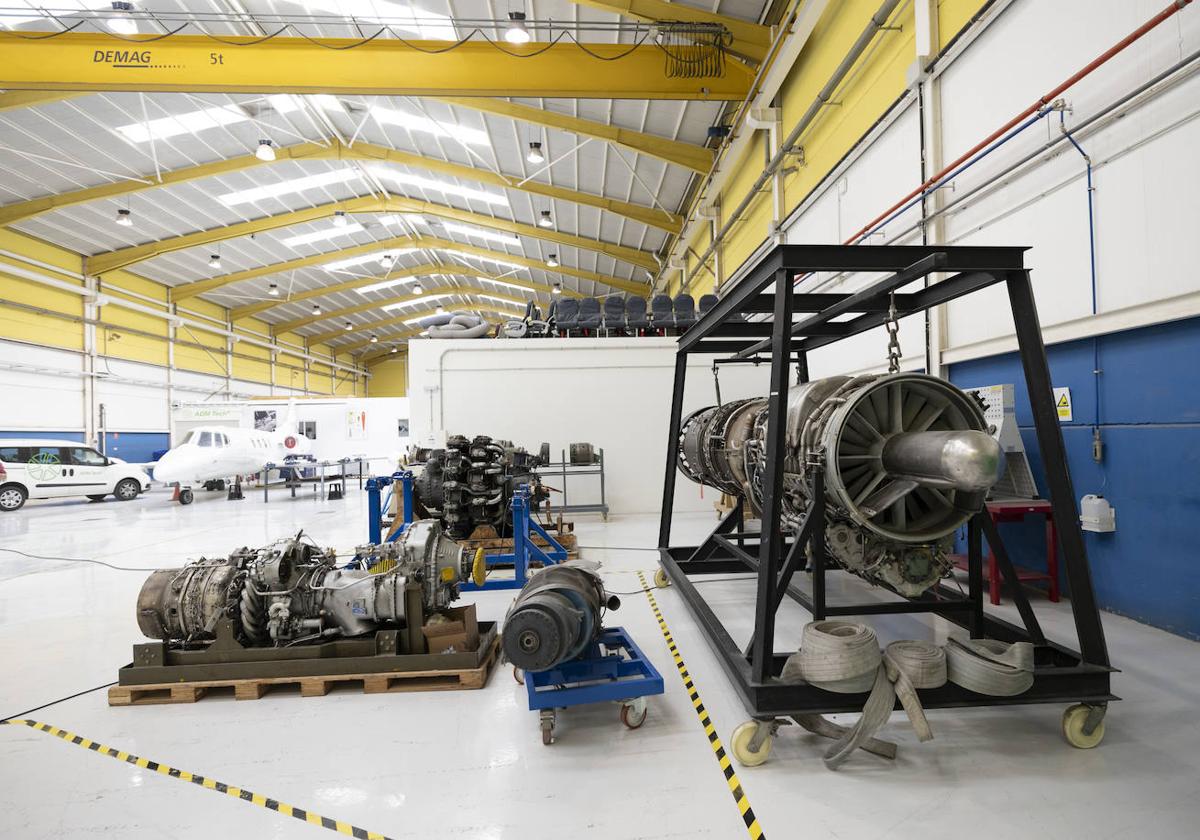
Una fábrica de aviones en medio del Atlántico
Transportes ·
Desde la planta de Binter en Gran Canaria se diseñan y arreglan pequeñas piezas para aerolíneas de todo el mundo, reduciendo tiempos y costes con una nueva vía de ingresosSecciones
Servicios
Destacamos
Transportes ·
Desde la planta de Binter en Gran Canaria se diseñan y arreglan pequeñas piezas para aerolíneas de todo el mundo, reduciendo tiempos y costes con una nueva vía de ingresosPara una empresa aeronáutica la posibilidad de fabricar sus propias piezas y reducir tiempos de espera –y los consiguientes costes– es básico. A nivel mundial la empresa más potente en este campo es la alemana Lufthansa, que en 1995 fundó LHT (Lufthansa Technik) para fabricar ... y reparar miles de piezas al año tanto para la propia aerolínea como para terceros, siguiendo los pasos de Air France. Pero Lufthansa tiene un hermano pequeño en España. Concretamente en la isla de Gran Canaria, desde donde la aerolínea Binter fabrica y repara más de 2.000 piezas diferentes para la propia compañía, pero el 20% de la producción es para otras.
La empresa, que se fundó en 2016 con solo seis empleados, cuenta ahora con 35 personas en plantilla, factura 3 millones al año (nada que ver con la compañía matriz, pero son una pata «estratégica» de la empresa) y ha conseguido que el 75% del total de sus piezas sean de producción propia y solo el 25% tenga que comprarlo fuera. En estos ocho años ADM Tech ha conseguido diferenciarse del resto de empresas del sector por la producción de pequeños componentes aeronáuticos a gran escala en lugar del textil y grandes piezas de otros fabricantes. «Las piezas pueden tardar en llegar de tres a cinco meses, mientras que si las hacemos aquí son cuatro días y se reducen muchísimo los precios», explica Luis Bernal, gerente de ADM Tech, en una visita a la planta que Binter tiene en Arinaga, al sureste de Gran Canaria.
Su modus operandi es muy práctico: observan cuáles son las piezas que más se rompen o se dañan antes y se empeñan hasta que las fabrican ellos mismos. Así han conseguido convertirse en una de las pocas empresas autónomas para reparación de ciertas partes del avión muy costosas, como los 'flaps', o en ser los únicos en España que reparan los sistema de antihielo de las alas o los empenajes (estabilizadores de la cola) para los modelos ATR72. En total, hoy la compañía es capaz de reparar más de 2.000 componentes aeronáuticos distintos. Pero no registran patentes, sino que generan documentos confidenciales que guardan bajo llave. «Mejoramos al doble o triple la durabilidad de ciertas piezas, el ahorro en fabricación es enorme, aunque la responsabilidad es solo nuestra», indica Bernal.
El gerente explica que conseguir repuestos fuera de Canarias «cuesta mucho, tanto económicamente como el tiempo que pasa para recibirlos». Por eso estar especializados en reparación y diseño propio les da mucha soltura a nivel de fabricación y de solución de averías. A Bernal, gestor y técnico de mantenimiento de profesión pero sobre todo de vocación, la fundación de ADM Tech le pilló ya con 60 años y ahora con 68 no piensa en la jubilación. «Lo bonito es ir creando innovación, no solo comprar por comprar», asegura.
Un ejemplo práctico. La aerolínea cuenta actualmente con 24 aviones, por lo que posee 48 generadores, ya que cada nave necesita dos de estos dispositivos para su funcionamiento. Cada generador tiene un coste aproximado de 11.000 euros y su fabricación lleva aproximadamente dos semanas de trabajo, es decir, «dos semanas que tienes un avión parado», señala Bernal. Unos plazos que se triplicarían si tuvieran que pedir esa pieza fuera, lo que obligaría a Binter a contar con más generadores de repuesto, con el consiguiente coste extra que eso supondría.
La planta de Telde permite una flexibilidad de diseño y control de sus naves poco usual en otras aerolíneas. Es el caso de sus aviones ATR (los que suelen usarse para viajes entre islas, más pequeños y con hélices), que vienen de fábrica con una capacidad de 78 asientos, pero Binter es capaz de modificar su estructura interna en un proceso que lleva aproximadamente seis meses de trabajo y los transforma en naves que transportan a 74 personas.
Y lo mismo ocurre con los Embraer, prediseñados para 140 pasajeros, pero que la aerolínea desmonta para que su capacidad sea de 132, con 79 centímetros de distancia entre filas en una configuración de asientos 2+2, para que así haya más espacio por persona y hueco suficiente para una maleta de mano en cabina por pasajero.
ADM Tech tiene cuatro áreas de trabajo: una dedicada al diseño, otra de producción, otra de reparación y otra de ensayos.
¿Ya eres suscriptor/a? Inicia sesión
Publicidad
Publicidad
Te puede interesar
Publicidad
Publicidad
Esta funcionalidad es exclusiva para suscriptores.
Reporta un error en esta noticia
Comentar es una ventaja exclusiva para suscriptores
¿Ya eres suscriptor?
Inicia sesiónNecesitas ser suscriptor para poder votar.